Gasification
What is Gasification?
Gasification is an Advanced Thermal Treatment technology that is characterised by the partial oxidation of the feed stock. Oxygen is added, but not in sufficient quantities to allow the substance to be completely oxidised and full combustion to occur. The partial combustion results in the production of 'Syngas' which can be used to substitute natural gas, chemicals, fertilisers, transportation fuels and hydrogen.
The gasification of solid materials is not a new concept - gasification first occurred in the late 1700s and early 1800s to produce tar. The types of gasification technologies which are used today have largely been developed over the last 20 years. It has been used extensively to manufacture fuels such as town or producer gas, which is a combustible gas produced by the gasification of coke in the presence of air and steam.
Gasification is not a commonly used process for MSW in the UK. It finds a greater application with certain relatively well defined biomass fuels, for example wood chips. It is only in recent years that gasification has been commercially applied to the treatment of MSW; however, large scale plants have been built and are in operation in Europe, North America and Japan
Inputs
Gasification is focused on treating the biodegradable based materials present in MSW (e.g. paper, card, putrescible waste, green waste, wood), as well as plastics as they have a high carbonaceous content. For this reason, non combustible materials and recyclables (typically metals and glass), are normally removed in a pretreatment stage as they can result in a reduction in the heat available for the process therefore affecting the process and operational efficiency.
In addition, depending on the technology employed, the feed material might require processing and pre-treatment to remove excess moisture and shredding to reduce the size. It is the preference (for most ATT processes) to treat only pre-processed residual MSW that makes these systems appropriate to be integrated into a wider municipal waste management strategy. ATT processes may be used in conjunction with other waste treatment technologies such as Mechanical Biological Treatment (MBT) and Mechanical Heat Treatment (MHT).
Many MBT/MHT plant are designed to produce a fuel stream (primarily composed of paper, card and plastics) as one of the outputs from the process. This is commonly referred to as Refuse Derived Fuel or RDF. Refuse Derived Fuel (RDF) and Solid Recovered Fuel (SRF) can be used as a feedstock for the gasification process, although large scale experience of this is relatively limited at present compared to incineration systems.
The Gasification Process
Following preparation, the feedstock will be added into the gasifier, where the organic material is converted by partial oxidation into a mixture of the energy rich synthetic gas or 'syngas'. This is comprised of carbon monoxide, hydrogen and methane. Typically, the gas generated from gasification will have a net calorific value (NCV) of 4 - 10 MJ/Nm3. The other main product produced by gasification is a solid residue of noncombustible materials (ash) which contains a relatively low level of carbon. For reference, the calorific value of syngas from gasification is far lower than natural gas, which has a NCV of around 38 MJ/Nm3.
The Gasification process is largely exothermic, some energy input may be required to begin and maintain the gasification process. The temperature of the process is important, typically the process will operate between 900-1100oC with air and 1000-1400oC with oxygen. Gasification with oxygen tends to result in a better quality of gas than gasification with air. The fuel value with air is approximately 4-6MJ/Nm3 and the fuel value with oxygen is approximately 10-18 MJ/Nm3, though this does depend on the calorific value of the feedstock used.
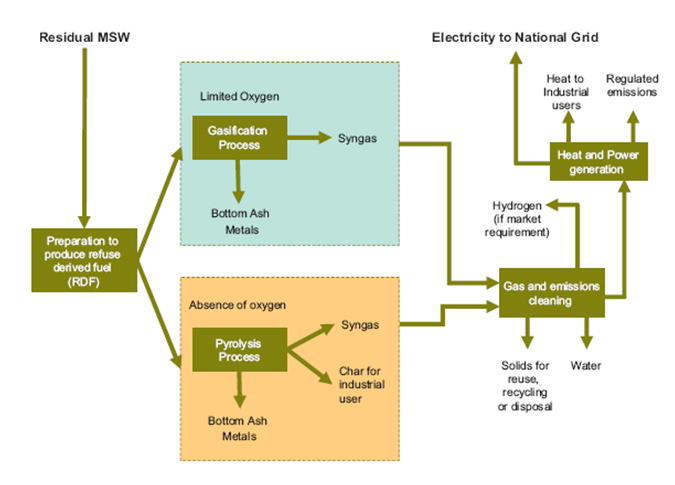
Although the precise details vary according to the details of design, the process normally works by the partial combustion of the material to provide heat which then decomposes what material is left. The four points below show the process elements the feedstock will go through in the gasification reactor:
- Drying by the addition of heat to remove the water vapour from the feedstock
- Gasification by the addition of heat to volatilize the organic components and produce the syngas, vapourised tars and solid carbon residue
- Gasification or combustion of the solid residue and tars, upgrading the syngas
- Combustion typically completes the process and provides for liberation and recovery of the energy value, this stage is not included where the products have some other use
Outputs
Most gasifiers produce a glass-like byproduct called slag, which is non-hazardous and can be used in roadbed construction and in roofing materials. Syngas also need to be cleaned to remove impurities such as sulphur, mercury, particulates and other trace minerals which can then be used for other chemical processes. The Syngas can then be used to substitute natural gas, chemicals, fertilisers, transportation fuels and hydrogen.
Reference